湿法、干-湿法纺丝的流程与基本概念
日期:2018-10-31 10:27
一、湿法纺丝的流程和基本概念
湿法纺丝的工序包括(图1-1):①制备纺丝原液;②将纺丝原液从喷丝头压出形成细流;③原液细流凝固成初生纤维;④初生纤维卷装或直接进行后处理。
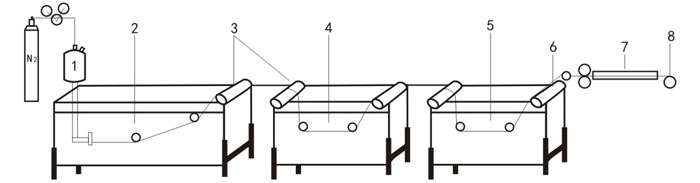
图1-1 聚酰亚胺或聚酰亚胺纤维湿法纺丝流程
1—聚酰胺酸或聚酰亚胺溶液;2凝固浴;3,6一纺丝导辊;4,5—水洗浴;7一后处理装置;8—络筒。
湿法纺丝(湿喷-湿纺)过程是将聚酰胺酸或聚酰亚胺纺丝原液从循环管道送至纺丝机,通过计量泵计量,然后经过滤器、连接管而进入喷丝头。喷丝头般采用金与铂的合金或钽合金材料制成,在喷丝头上有规律地分布若干孔眼,孔径为0.04~0.08mm。从喷丝头孔眼中压出的原液细流进入凝固浴,原液细流中的溶剂向凝固浴扩散,凝固浴通常由水和纺丝原液的溶剂按一定比例组成,水作为凝固剂向细流渗透,从而使原液细流达到临界浓度,在凝固浴中析出而形成初生纤维,湿法纺丝过程中的扩散和凝固是物理化学过程。湿法纺丝时可用较稀的聚合物溶液,挤出时表观黏度处于2~500Pa·s范围,溶液固含量在3%-30%之间变化,凝固浴温度通常不超过0~100℃。最大纺丝速度由于凝固浴中流体阻力而受到限制,很少超过50-100m/min。湿法纺丝是最复杂的纺丝操作,在纺丝工艺方面,所涉及的关键技术包括如何确立最佳纺丝工艺参数(如纺速、凝固浴组成、原丝干燥条件、酰亚胺化过程控制、高温拉伸条件等)以获得具有最佳形态结构的纤维以及溶剂和凝固浴的各溶剂组分的有效回收。
二、干-湿法纺丝的基本概念和流程
将干法纺丝与湿法纺丝的特点结合起来的化学纤维纺丝方法,又称干喷湿法纺丝,简称干-湿法纺丝。干一湿法纺丝是20世纪60年代发展起来的纺丝新方法,纺丝原液从喷丝头喷出后先经过一段空气层(3~100mm,通常为20-30mm),然后进入凝固浴,经水洗、干燥、后处理等工艺过程制得聚酰亚胺纤维。实际上,干一湿法纺丝工艺研究的问题与湿法纺丝所研究的相似,其最重要的问题就是如何获得具有最佳形态结构(对于凝固浴的组成和条件非常敏感)的初生纤维。
干-湿法纺丝工艺所涉及的关键技术也与湿法纺丝的相似,只是干-湿法比湿法纺丝增加了一段在空气中的喷丝及拉伸过程,因此空气层长度是干一湿法纺丝工艺中的重要参数之一。空气层长度是指干一湿法纺丝过程中纺丝原液细流从喷丝头喷出后,到进入凝固浴时,在垂直喷丝头方向上经过的长度。这一过程是纺丝原液进入凝固浴形成初生纤维所必须经历的路径,在这一阶段,纤维束的流动方向与纺丝液进入凝固浴的方向以及重力方向一致,横截面方向上受到的外力较为均匀,使得纤维在成型过程中横截面形状可以保持均匀,所以这一部分的长度和气流状态对纤维横截面的形状以及性能影响很大。采用干-湿法纺丝时,纺丝原液细流能在空气中经受显著的拉伸,拉伸区长度远超过液流胀大区的长度。在这样长距离内发生的液流轴向形变,速度梯度不大,实际上在胀大区没有很大的轴向形变。与此不同,湿法纺丝时原液细流从喷丝头喷出后,拉伸在很短的距离内发生,速度梯度很大,液流胀大区发生剧烈的形变,在喷丝孔附近,较细的丝条在拉伸下就会发生断裂。因此,采用干一湿法纺丝时可提高喷拉比和纺丝速度。干-湿法纺丝的丝速可达600-1200m/min,远比湿法纺丝纺速高,而且可以使用孔径较大(为0.15~0.3mm)的喷丝头。而纺丝原液的浓度和黏度则可以像干纺时那样高,采用干-湿法纺丝还能较有效地控制纤维的微结构形成过程。干法纺丝时,因受溶剂的挥发速度所限,液流的凝固速度往往很慢。干-湿法纺丝时,正在被拉伸中的液流(纤维)进入凝固浴,凝固速度和纤维微结构可借调节凝固浴组成和温度而在很宽的范围内改变。干-湿法纺丝虽兼具干法纺丝和湿法纺丝的优点,但液流容易沿喷丝头表面漫流,这种现象与高聚物溶液的黏弹性、表面张力、喷丝孔几何形状和挤出液流的形变速度有关。
干-湿法纺丝工艺所涉及的关键技术也与湿法纺丝的相似,只是干-湿法比湿法纺丝增加了一段在空气中的喷丝及拉伸过程,因此空气层长度是干一湿法纺丝工艺中的重要参数之一。空气层长度是指干一湿法纺丝过程中纺丝原液细流从喷丝头喷出后,到进入凝固浴时,在垂直喷丝头方向上经过的长度。这一过程是纺丝原液进入凝固浴形成初生纤维所必须经历的路径,在这一阶段,纤维束的流动方向与纺丝液进入凝固浴的方向以及重力方向一致,横截面方向上受到的外力较为均匀,使得纤维在成型过程中横截面形状可以保持均匀,所以这一部分的长度和气流状态对纤维横截面的形状以及性能影响很大。采用干-湿法纺丝时,纺丝原液细流能在空气中经受显著的拉伸,拉伸区长度远超过液流胀大区的长度。在这样长距离内发生的液流轴向形变,速度梯度不大,实际上在胀大区没有很大的轴向形变。与此不同,湿法纺丝时原液细流从喷丝头喷出后,拉伸在很短的距离内发生,速度梯度很大,液流胀大区发生剧烈的形变,在喷丝孔附近,较细的丝条在拉伸下就会发生断裂。因此,采用干一湿法纺丝时可提高喷拉比和纺丝速度。干-湿法纺丝的丝速可达600-1200m/min,远比湿法纺丝纺速高,而且可以使用孔径较大(为0.15~0.3mm)的喷丝头。而纺丝原液的浓度和黏度则可以像干纺时那样高,采用干-湿法纺丝还能较有效地控制纤维的微结构形成过程。干法纺丝时,因受溶剂的挥发速度所限,液流的凝固速度往往很慢。干-湿法纺丝时,正在被拉伸中的液流(纤维)进入凝固浴,凝固速度和纤维微结构可借调节凝固浴组成和温度而在很宽的范围内改变。干-湿法纺丝虽兼具干法纺丝和湿法纺丝的优点,但液流容易沿喷丝头表面漫流,这种现象与高聚物溶液的黏弹性、表面张力、喷丝孔几何形状和挤出液流的形变速度有关。
上一篇:聚酰亚胺纤维的一步法、两步法纺丝
下一篇:湿法、干一湿法纺丝的差别